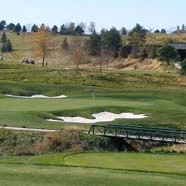
When we think of traditional examples of positive communication, the communication normally precedes the subject we’re communicating about. We want all the signals straight before we break ground, right? There is limited value to having everyone on the same page after the fact.
There is no substitute for solid planning, but we all know that life isn’t always like that. On those occasions when the best-laid plans go out the window, effective communication on the fly, in the field, becomes especially important. And when we look closely at a successful project, the decision-making was usually a mix of what A finished complex from Jefferson City CC in Missouri.we got right ahead of time, and what we got right along the way.
CLICK HERE TO CHECK OUT BOB'S BLOG
We’ve just finished up the first of a three-phase renovation plan for Indian Creek Golf Course in Elkhorn, Neb., where twice in the space of 6 months we were obliged to depart from the norm, to depart from convention and our “best-laid plans”, in order to get the job done and achieve what the client sought to achieve. In one case, the client educated us (as to their firm priorities); in the other, the process itself did the teaching, and all involved became avid learners.
Indian Creek is a solid, 27-hole public facility on super terrain — rolling prairie cut by natural water features and dotted with stands of hardwood. We originally went out there to look at the bunkering, but we ultimately agreed the greens — which had poa annua issues typical of 20-year-old bentgrass putting surfaces — needed a more uniform challenge in terms of contour. We did quite a comprehensive renovation master plan that included some rerouting, as well.
However, when we priced the job, it was more than the client wanted to spend. This was the fall of 2008, when an investment of any significant size was a big risk. So we dialed things back: After lengthy consultation with the client, we discarded the grand plan and resolved to do the bunker renovations, 9-holes at a time, over three years. The greens would not be recontoured but would be reseeded, with T-1 bentgrass, in order to address the poa issues.
This required fumigation, of course, which will call for some alternative planning in the coming years. The use of methyl bromide to sterilize greens prior to reseeding has been the subject of increased regulation for a while now. According to our friends at Hendrix and Dail (HD), the fumigation experts, the use of methyl bromide in hot gas applications will change considerably at the end of this year. Starting Jan. 1, 2011, the product label will require increased safety precautions for applicators and reductions in allowable rates (50% or more). These restrictions alone greatly reduce the product’s viability on A newly renovated green complex in Omaha.golf greens. In 2012, restrictive buffer zones will be added. This will effectively end the practical application on golf courses in general – except for maybe those properties located in the middle of a corn field with no human dwellings within several thousand feet!
In any case, Phase I of the Indian Creek bunker renovation and green-reseeding effort began July 13, 2010, with our work on the Blackbird nine. The superintendent at Indian Creek, Jim Nedrow, had prepared in advance for the fumigation. It’s unusual to fumigate so early in the construction process. Normally, you’d like to have all the green surrounds finished, all the irrigation done, then fumigate and seed.
But the folks at Indian Creek were adamant about having the new greens playable in the spring of 2011 to minimize further revenue loss due to course closure. They wanted to set aside the fall of 2010 for additional grow-in. So, hearing this loud and clear, all parties worked hard to meet deadlines and the contractors at Golf Creations did an excellent job working from, and working around, the existing green footprints.
One of the bunker renovation’s major goals had always been limitation of sand movement and contamination, which minimizes long-term sand maintenance and replacement costs. To accomplish this, we recommended implementing a flat-bottom style, which we had employed successfully in similar climates. We also debated as a group about the necessity of bunker liners — a product not typically needed with the flatter style. At $1.50 to $3 per square foot, it’s also a considerable project expense when working on a controlled budget.
To help make a decision, the owner rebuilt a single test bunker beside the club’s practice green the previous fall, which helped demonstrate the effectiveness of the flat style and liner. But it wasn’t until the owner made a significant investment in white sand that the commitment was made to include the liner, initially as a sort of insurance to keep the native soils from migrating up and discoloring the new sand.
Here’s where it gets interesting. As the bunkers were being built, the effectiveness of the liner (for minimizing erosion) became more evident, giving the owner more comfort in flashing the sand up on the faces. This became important for visibility (of the sand) on such a hilly site, and ultimately led to an adjustment in the bunker style towards the project’s end.
As these later bunkers were completed, with their higher-flashed sand and more sculpted edges — a dramatic style we had implemented with great success at Jefferson City (Mo.) Country Club — a decision was made to go back to several of the original bunkers and take their edges up another foot, which will actually be completed this winter by Nedrow’s crews. It’s unfortunate that this revelation took so long. Nevertheless, it will result in a much more interesting final product and ultimately a more satisfied client – who, by the way, should be commended for his willingness to get it right.
Bottom line: We broke a cardinal rule of bunker renovation — we changed the bunker style in the middle of construction. That’s generally a no-no, but in this case it was the right thing to do.
Now, when I tell this story, it almost sounds like we were experimenting at our client’s expense. But I don’t see it that way. We’ve done so many bunkers, in so many different styles, using so many different construction techniques that we know there is not always a single, concrete answer. We’re comfortable making changes on the fly and will encourage it when we’re convinced it will better the project. It’s one reason you hire experienced architects and contractors.
But I keep coming back to the communication angle. We enjoy an excellent, open relationship with the owner and the superintendent in Elkhorn. In planning and prepping for this work, we had already talked through a host of changes in strategy and scope, some according to convention, some not. In this context, tackling what were big changes in the field just doesn’t seem like such a big deal. And we’re that much better prepared for Phase II!
Latest from Golf Course Industry
- Heritage Golf Group acquires North Carolina courses
- Editor’s notebook: Green Start Academy 2024
- USGA focuses on inclusion, sustainability in 2024
- Greens with Envy 65: Carolina on our mind
- Five Iron Golf expands into Minnesota
- Global sports group 54 invests in Turfgrass
- Hawaii's Mauna Kea Golf Course announces reopening
- Georgia GCSA honors superintendent of the year